Die Casting Automotive: Revolutionizing the Auto Industry
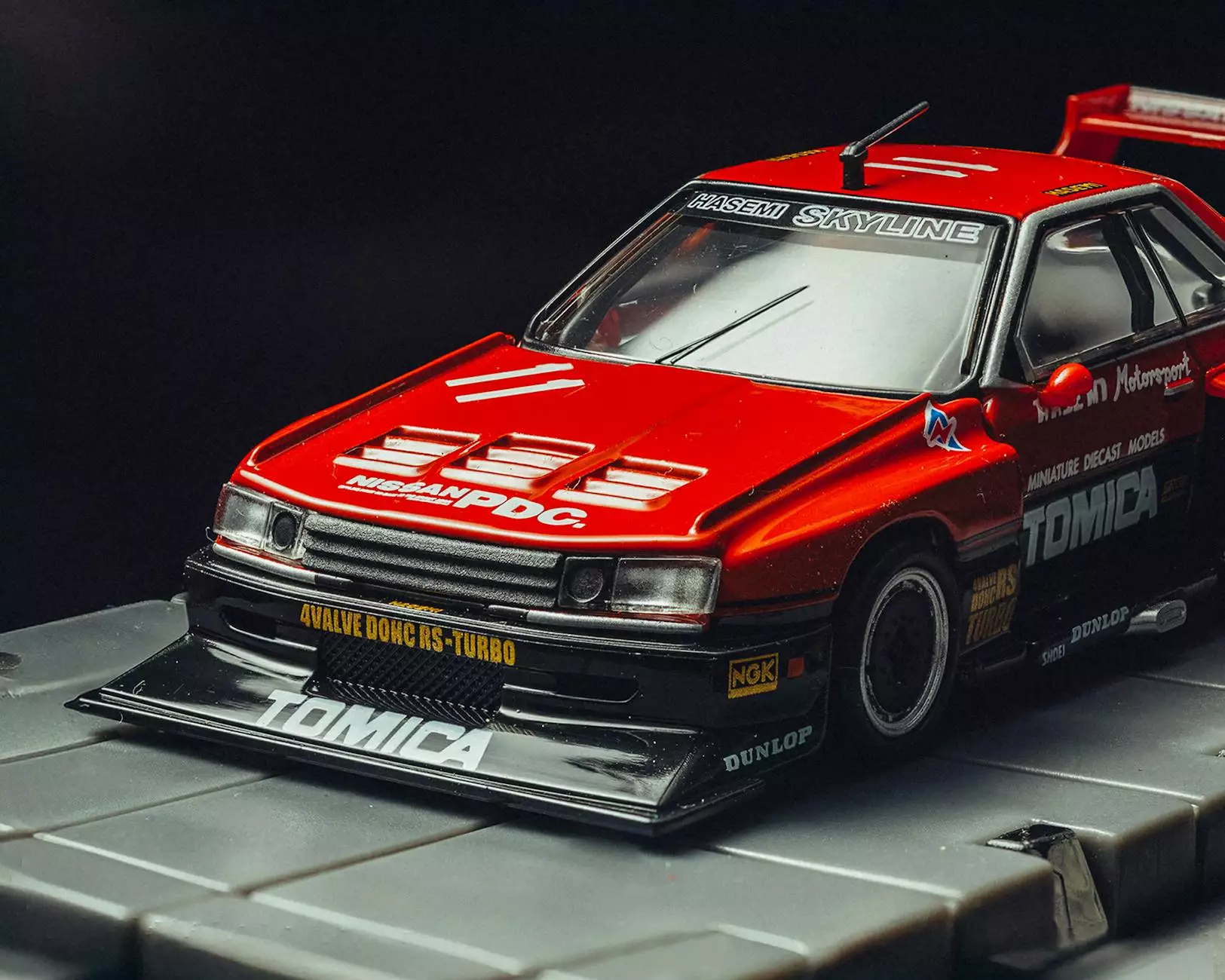
The automotive industry is undergoing a significant transformation driven by technological advancements, and at the forefront of this evolution is die casting automotive technology. This innovative manufacturing process is crucial for producing high-quality automotive components with precision and efficiency.
Understanding Die Casting
Die casting is a metal casting process that involves forcing molten metal into a mold cavity under high pressure. This technique is renowned for creating complex shapes while maintaining durability and surface finish. In the context of the automotive sector, die casting enables manufacturers to produce lightweight, strong parts that contribute to fuel efficiency and reduced emissions.
The Importance of Die Casting in Automotive Applications
With the automotive industry constantly demanding lighter and stronger materials, die casting automotive has emerged as a vital technology. Here are several key reasons why this process is indispensable in automotive manufacturing:
- Weight Reduction: Die casting allows for the production of lighter components, which is vital for enhancing vehicle performance and fuel efficiency.
- Complex Geometries: The method permits the creation of intricate designs that are often impossible to achieve with other manufacturing techniques.
- High Dimensional Accuracy: Components produced through die casting maintain tight tolerances, minimizing the need for additional machining processes.
- Cost Efficiency: High-volume production of parts via die casting can significantly reduce per-unit costs, making it an economically viable option.
- Material Versatility: Die casting can accommodate various metals, including aluminum and zinc, which are preferred for their strength and lightweight characteristics.
Die Casting Process: Step-by-Step
The die casting process involves several meticulous steps, each contributing to the final quality of automotive components. Understanding these steps offers insight into why die casting is preferred in the auto industry:
1. Mold Preparation
The first crucial step involves crafting high-quality molds that will hold the molten metal. These molds are typically made from steel or iron and are designed to withstand high temperatures and pressure.
2. Melting Metal
Next, the selected metal (often aluminum or zinc) is melted in a furnace at high temperatures. The molten metal must reach the ideal viscosity for optimal flow into the mold.
3. Injection of Molten Metal
Once adequately melted, the molten metal is injected into the mold cavity under immense pressure. This rapid injection ensures that the metal fills every part of the mold, creating a detailed component.
4. Cooling and Solidification
After the mold is filled, it’s cooled rapidly to allow the metal to solidify. Cooling time can vary based on the thickness of the part and the metal used.
5. Ejection
Once solidified, the mold opens, and the casting is ejected. At this stage, any excess material or imperfections can be trimmed or machined if necessary.
6. Finishing Processes
Finally, the die casted parts may undergo various finishing processes including painting, coating, or additional machining to meet specific design requirements.
Key Benefits of Using Die Casting in Automotive Manufacturing
The advantages of utilizing die casting automotive technology extend far beyond mere cost efficiency. Let's dive deeper into these benefits:
- Increased Production Rate: Die casting is highly efficient, allowing for the mass production of parts without sacrificing quality.
- Reduced Waste: The die casting process generates minimal waste, ensuring that materials are used effectively.
- Enhanced Mechanical Properties: Components produced via die casting exhibit exceptional mechanical strength, which is critical for automotive applications.
- Improved Surface Finish: Die cast parts often require less surface finishing, saving time and labor costs.
- Consistent Quality: This method ensures uniformity and repeatability, essential for large-scale automotive production.
Applications of Die Casting in the Automotive Industry
Die casting plays a pivotal role in producing various automotive components. Here are some common applications:
- Engine Blocks: The engine block is one of the most crucial parts of a vehicle, and aluminum die casting is often used for its lightweight and strength.
- Transmission Housings: Die-cast transmission housings provide the necessary durability and safety while remaining lightweight.
- Suspension Components: Components like control arms and brackets are commonly die-cast to withstand the stresses of road conditions.
- Electronic Housings: With the rise of electric vehicles, die casting is used to create housings for electronic components that require thermal management.
- Body Panels: Some body components can be effectively produced through die casting, contributing to overall vehicle aesthetics and performance.
Challenges and Solutions in Die Casting for Automotive
While die casting presents numerous advantages, there are challenges that manufacturers must navigate:
- Initial Cost: The cost of manufacturing molds can be high. However, this is often offset by the volume of production and long-term savings.
- Heat Treatment: Some die-cast parts may require heat treatment to achieve desired mechanical properties. This adds an additional step to the manufacturing process.
- Alloy Selection: Choosing the right metal alloy is crucial for the application. Automotive manufacturers must analyze the properties required for their specific needs.
To address these challenges, companies can invest in advanced technologies, streamline their processes, and continuously innovate material selection.
Future Trends in Die Casting Automotive
The future of die casting automotive looks promising with the emergence of new technologies and processes:
- Automation: Increasing automation in die casting processes is expected to enhance precision and efficiency further.
- 3D Printing: Integration of 3D printing technologies may allow for quicker prototyping and mold-making processes.
- Eco-Friendly Practices: The industry is moving towards more sustainable practices, including the use of recycled materials in die casting.
- Innovative Alloys: Research into new alloys that provide better performance and lower weight will impact future designs in automotive manufacturing.
Conclusion
The die casting automotive industry is poised for growth and transformation as it adapts to the demands of modern vehicles. As manufacturers like DeepMould harness the power of die casting technology, the benefits in efficiency, cost-effectiveness, and material performance will undoubtedly shape the future of transportation. Organizations that prioritize die casting in their manufacturing processes will be at the forefront of innovation, leading to smarter, safer, and more sustainable automotive solutions.
As the automotive industry evolves, die casting remains a cornerstone technology, making it more relevant than ever in creating the vehicles of tomorrow.