Understanding Rapid Prototyping Injection Moulding for Modern Businesses
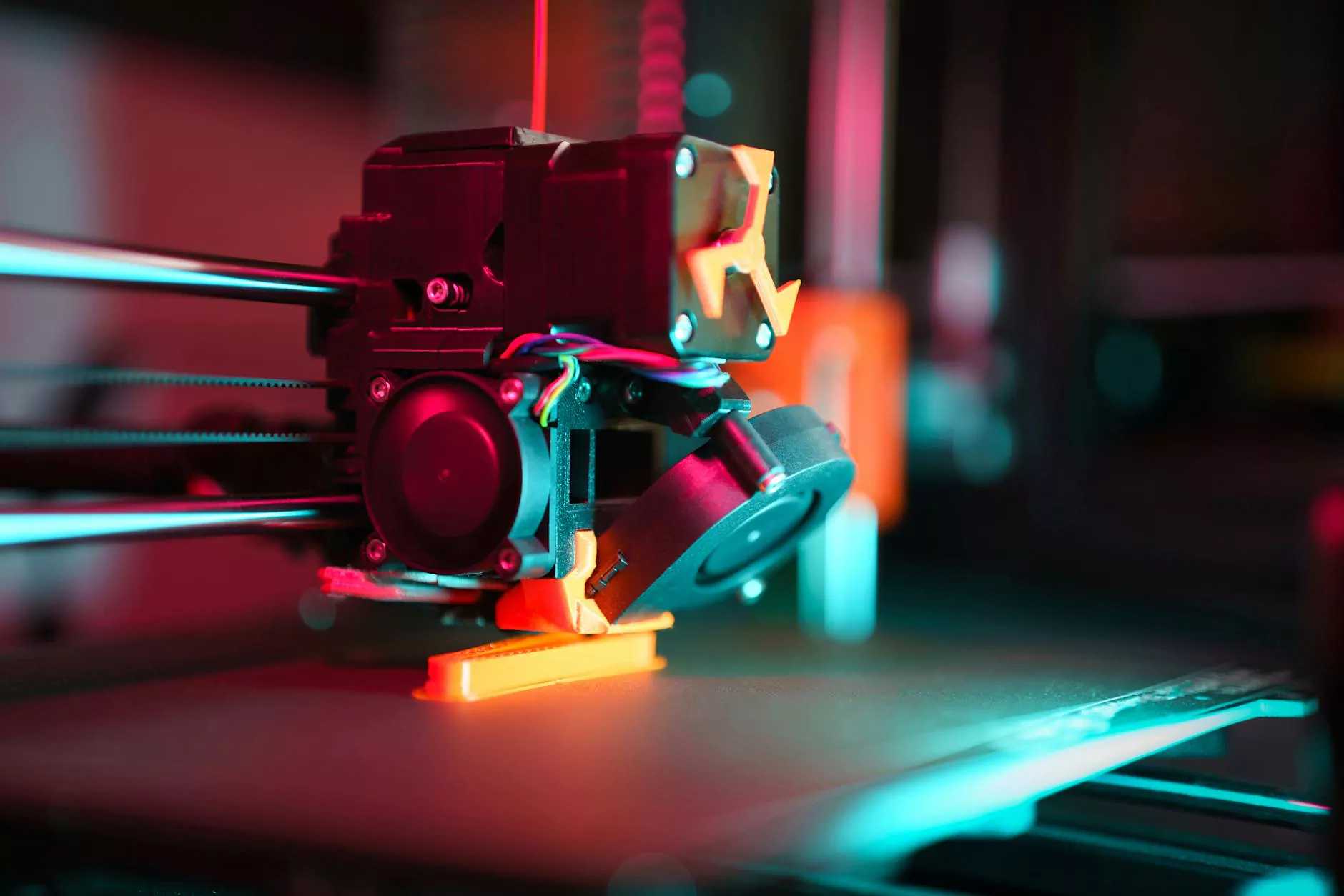
In today's competitive environment, businesses are constantly seeking innovative methods to streamline production processes and enhance product quality. One of the most effective approaches to achieve these goals is through rapid prototyping injection moulding. This technology not only accelerates product development but also reduces costs and improves overall efficiency.
What is Rapid Prototyping Injection Moulding?
Rapid prototyping injection moulding is a specialized process that uses injection moulding technology to create prototypes in a shortened timeframe. By employing this method, manufacturers can quickly turn concepts into tangible products, allowing for testing and modifications before full-scale production. This technique combines the speed of rapid prototyping with the power and versatility of injection moulding, producing high-quality, functional parts that can be used for testing, validation, and market introduction.
Key Benefits of Rapid Prototyping Injection Moulding
The advantages of using rapid prototyping injection moulding are numerous, making it an essential tool for businesses in various industries. Below are some of the major benefits:
- Speed: Rapid prototyping allows businesses to compress timelines, turning ideas into prototypes in a matter of days rather than weeks or months.
- Cost-Effective: This method significantly reduces the costs associated with traditional prototyping methods, allowing for multiple iterations without breaking the bank.
- Design Validation: Prototypes produced through this process can be tested and validated, enabling businesses to refine their designs based on actual performance and feedback.
- Material Versatility: A variety of materials can be used in rapid prototyping, providing businesses with flexibility in achieving the desired characteristics for their products.
- Reduced Waste: The efficiency of the injection moulding process minimizes material waste, aligning with sustainable manufacturing practices.
How Rapid Prototyping Injection Moulding Works
The process of rapid prototyping injection moulding involves several key steps, making it critical for manufacturers to understand the workflow:
Step 1: Conceptualization and Design
The first step is to develop a detailed design for the prototype using Computer-Aided Design (CAD) software. This digital model acts as a blueprint for the prototype.
Step 2: 3D Printing of Moulds
Using 3D printing technology, manufacturers create the moulds for injection. This rapid creation of moulds is a significant advantage, as it allows for quick iterations and changes to the design.
Step 3: Injection Moulding
Once the mould is ready, the chosen material is injected into the mould under high pressure, allowing it to take shape. This step produces the actual prototype, which can be physical and functional for various tests.
Step 4: Testing and Refinement
The prototype undergoes various tests to ensure it meets the required specifications. Feedback collected during this phase is crucial for making necessary modifications before the final product is manufactured.
Applications of Rapid Prototyping Injection Moulding
Businesses across different sectors can leverage rapid prototyping injection moulding for various applications. Here are a few industries that benefit from this technology:
1. Automotive Industry
The automotive sector frequently uses rapid prototyping to test and refine new parts, leading to improved vehicle performance and safety features. Manufacturers can rapidly produce components for testing in extreme conditions.
2. Consumer Electronics
In an industry that thrives on innovation, rapid prototyping allows for the swift development of electronic enclosures and components, facilitating the fast-paced release of new products.
3. Medical Devices
Medical companies rely on prototyping to create precise and functional devices quickly. Rapid prototyping enables the design and testing of medical solutions that adhere to strict regulations.
4. Consumer Products
Whether it’s kitchenware, furniture, or personal care products, businesses benefit from rapid testing and market readiness, securing a competitive edge.
Choosing the Right Partner for Rapid Prototyping Injection Moulding
Selecting the right manufacturing partner is crucial to the success of your rapid prototyping injection moulding projects. Aspects to consider include:
- Experience: Look for a company with a proven track record in rapid prototyping and injection moulding.
- Technical Expertise: Ensure that the partner has the necessary technical skills and equipment to handle your specific needs.
- Material Options: A wide range of material choices can affect the durability and functionality of your prototypes. Choose a partner that offers various options.
- Customer Support: Strong communication and support throughout the prototyping process can significantly enhance project outcomes.
- Turnaround Times: Evaluate the company’s capability to meet your deadlines without compromising quality.
Future of Rapid Prototyping Injection Moulding
As technology continues to evolve, the future of rapid prototyping injection moulding looks promising. The integration of advanced technologies such as artificial intelligence and machine learning is likely to further enhance the efficiency and capabilities of prototyping processes. Changes in materials science may also introduce new possibilities in terms of the properties and functionalities of the produced prototypes.
Moreover, as businesses increasingly prioritize sustainability, innovations in eco-friendly materials and waste reduction techniques in rapid prototyping will gather more attention. Companies that adapt to these trends will not only improve their manufacturing processes but also enhance their market position.
Conclusion
In conclusion, rapid prototyping injection moulding represents a transformative approach for businesses aiming to innovate and compete effectively in today’s market. By understanding its benefits, processes, and applications, companies can leverage this technology to enhance product development, minimize risks, and accelerate time-to-market. For any business looking to stay ahead, investing in rapid prototyping injection moulding is not merely an option; it is a strategic necessity.
To explore how rapid prototyping injection moulding can benefit your designs and accelerate your projects, visit DeepMould.net for more insights.