Mastering Injection Molding Tooling Design: A Comprehensive Guide
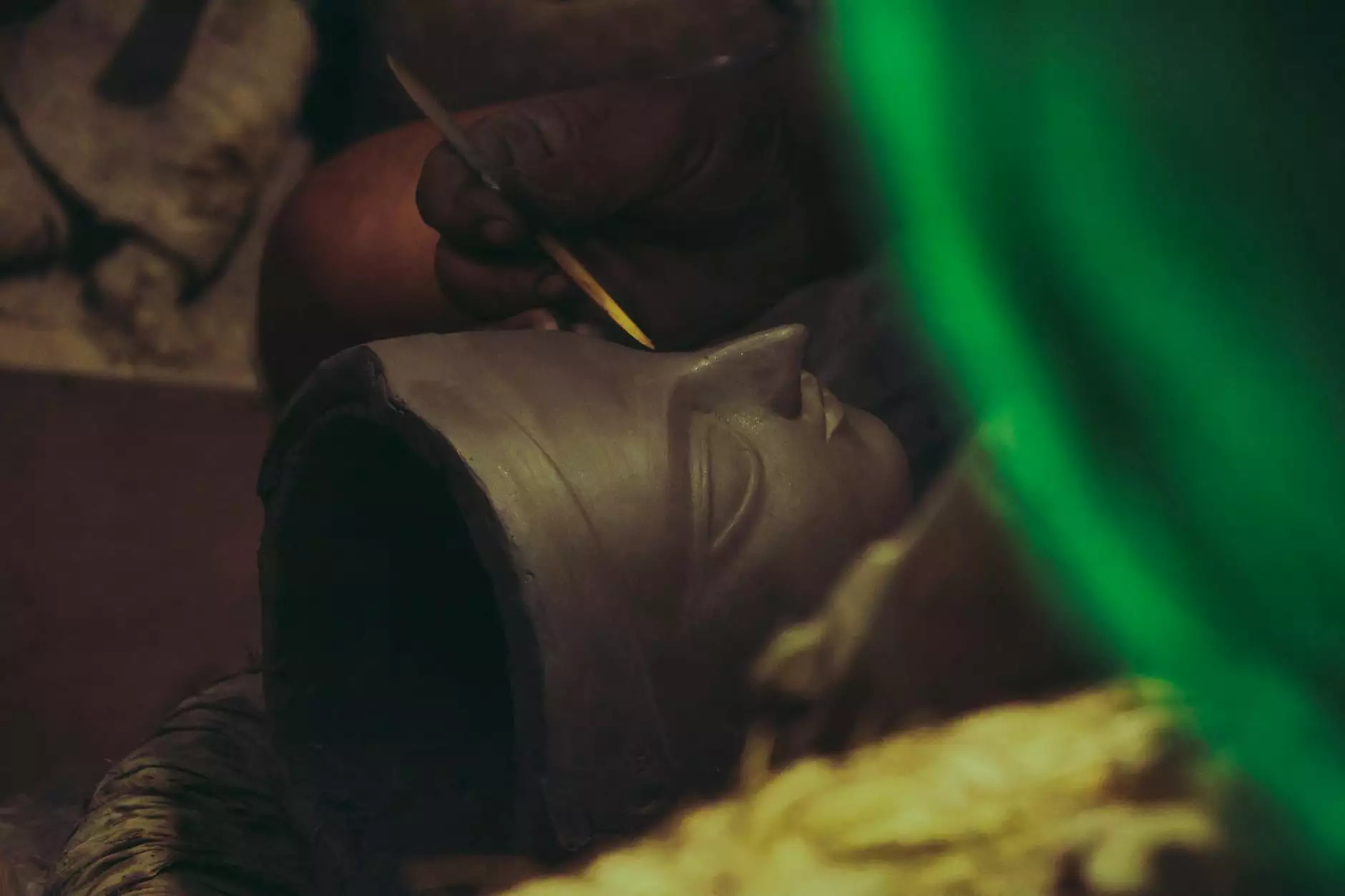
Injection molding tooling design is a critical aspect of the manufacturing process that involves creating molds for producing parts through injection molding. This method offers a myriad of benefits, including high production efficiency, precision, and the ability to create complex geometries. In this extensive article, we will explore the nuances of tooling design, its significance in metal fabrication, and best practices to achieve optimal production outcomes.
The Fundamentals of Injection Molding Tooling Design
At its core, injection molding is a process where molten material, typically plastic, is injected into a mold cavity to form specific shapes. The tooling design encompasses all the elements of the mold necessary to create the desired part. Understanding the different components of tooling design is pivotal for engineers and manufacturers alike.
Components of Injection Molding Tooling
Tooling for injection molding typically consists of several components, including:
- Mold Base: Provides the structure to hold the cavity and core. It consists of the mounting blocks and is usually made from high-strength steel.
- Cavity: The hollow space that gives the part its shape. The design must consider draft angles and surface finish.
- Core: Complements the cavity to create complex internal shapes. It requires precision and careful design to ensure accurate part formation.
- Cooling System: Integral in regulating the temperature of the mold to ensure quick solidification and minimize cycle time.
- Ejector System: Mechanism to remove finished parts from the mold without damage.
Importance of Tooling Design in Efficient Manufacturing
The significance of effective injection molding tooling design cannot be overstated. Proper tooling design leads to several competitive advantages, including:
- Cost Efficiency: Well-designed molds reduce production costs by minimizing material waste and downtime.
- Quality Control: Precision tooling directly impacts the quality of the final product, ensuring consistency and reliability.
- Production Speed: Efficient cooling and ejection mechanisms contribute to shorter cycle times, enhancing overall productivity.
The Design Process for Injection Molding Tooling
Creating a robust injection molding tooling design requires a systematic approach that includes several phases:
1. Conceptualization and Requirements Gathering
Initially, designers must gather requirements based on the product specifications and production targets. This phase includes:
- Understanding the material properties.
- Establishing tolerances and surface finishes.
- Defining production volume requirements.
2. Mold Design and Simulation
Utilizing CAD software, designers create a digital mold model, simulating various conditions to predict how the mold will perform during production. This stage is crucial for identifying potential defects.
3. Prototyping and Testing
Before finalizing the tooling, creating a prototype allows manufacturers to test the mold’s design. This is an invaluable step for assessing fit, function, and potential improvements.
4. Tool Fabrication
Once the design is validated, the tooling is manufactured. This stage involves precision machining of various components, requiring the use of advanced manufacturing technologies.
5. Final Assembly and Testing
The last step encompasses the assembly of all tooling components, followed by rigorous testing to ensure functionality and quality before the tooling is used in production.
Challenges in Injection Molding Tooling Design
Despite its advantages, injection molding tooling design presents several challenges, including:
- Complex Geometries: Creating molds for intricate designs may require specialized tooling techniques.
- Material Selection: Choosing the right materials for the mold can affect durability and performance.
- Cooling Efficiency: Designing an effective cooling system is crucial to minimize cycle times without compromising part quality.
Advancements in Injection Molding Technology
The field of injection molding tooling design is continually evolving. Recent advancements have significantly impacted design efficiency and manufacturing outcomes:
3D Printing of Molds
3D printing technology has revolutionized mold production. It allows manufacturers to create complex mold shapes quickly and economically, resulting in reduced lead times.
Computer-Aided Engineering (CAE)
CAE tools enable engineers to simulate the injection molding process, assessing the performance of the design before actual production, thus minimizing trial-and-error stages.
Integration of IoT in Tooling
Internet of Things (IoT) integration ensures real-time monitoring of tooling performance, providing valuable data for predictive maintenance and operational optimization.
Sustainability in Injection Molding Tooling Design
As environmental concerns continue to rise, the injection molding tooling design industry is making strides toward sustainability. Strategies include:
- Use of Recyclable Materials: Opting for recyclable plastics in production.
- Energy Efficiency: Designing molds that require less energy during the manufacturing process.
- Waste Reduction: Streamlining processes to minimize scrap and waste produced during the molding cycle.
Conclusion
In conclusion, mastering injection molding tooling design is essential for achieving optimal efficiency in manufacturing, particularly in the metal fabrication industry. By understanding the intricacies of the design process, potential challenges, and recent advancements, businesses can better position themselves in a competitive market. Embracing these insights allows for innovation, cost savings, and product quality that meets the highest standards. For those in the metal fabricators category, investing in sophisticated tooling design is not just beneficial; it is imperative for success in today’s manufacturing landscape.
For more information about quality tooling and manufacturing solutions, visit DeepMould.net.